Premier Microgrid for Manufacturers
Since 1905, G&W Electric has helped power the world with innovative power systems solutions and products.
For the past few years, recurring electric supply problems from the grid have resulted in significant costs and production disruptions, impacting revenue for G&W Electric.
Alarmed by the huge cost of these disruptions, G&W decided to find a solution and improve their profitability.
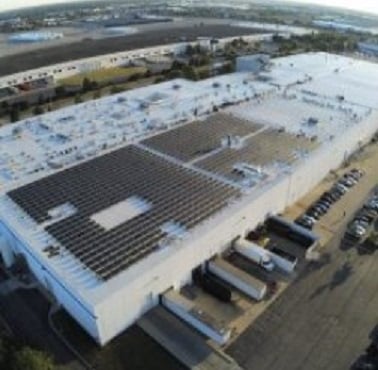
G&W Electric is a manufacturer of medium voltage utility power equipment in Bolingbrook, IL. The plant covers over 371,000 sq ft of space. Their 24x7 manufacturing operations include injection molding, ceramics, assembly, office, warehouse, and engineering / R&D. Even short power outages can cost millions of dollars in lost production time and materials.
Being in the electric industry, G&W is well positioned to evaluate alternative power options for their manufacturing operations. They already had an on-site backup electric generator, but it took too long to begin producing power and could create power quality issues while it was running.
Recent advances in hardware and software provided an opportunity to design a state-of-the-art alternate power system for their needs. Offering much more than emergency power generation, G&W completed a microgrid in 2022 that added solar generation and a flywheel to the existing generator, along with battery energy storage to provide backup power, bill savings, and new revenues.
Significant incentives helped pay for the microgrid. Illinois offers exceptional incentives for storage and solar components and are paid by the utilities. The G&W project earned a $2.6M cash rebate for the project from Commonwealth Edison, through Illinois’ Smart Inverter Rebate program. Federal incentives included Investment Tax Credits and accelerated MACRS depreciation.
When electric outages occur, the G&W microgrid automatically isolates itself from the main grid to allow continuing operations by doing an instantaneous switch to backup power. The microgrid saved $2 million in avoided losses in the first year of operation alone. As of November 2024, the system has been in operation for two years, during which time eleven outages have been prevented, avoiding significant downtime, costs and lost productivity.
The 2MW battery energy storage system is managed by Intelligent Generation (IG), a third-party company specializing in energy storage optimization. IG leverages revenue and bill savings opportunities by doing strategic dispatch of stored energy. IG has saved G&W $420,000 per year in electric bill reductions and earns $250,000 annually from utility grid ancillary services market opportunities.
The projected ROI of the system is under 4 years. Once paid off, the microgrid assets will continue to generate revenue to improve G&W profitability through its estimated 25-year lifecycle.
Key components of the system include:
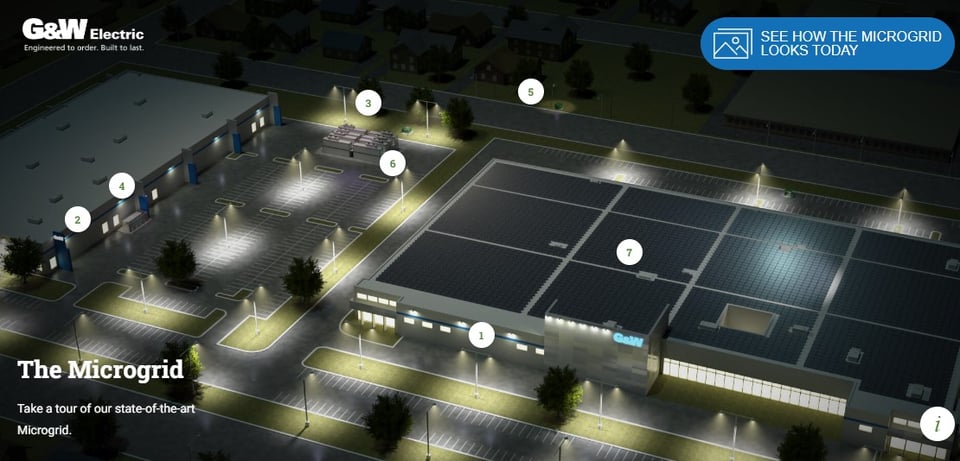
Solar Panel Array
A two-megawatt solar farm with nearly 6,000 solar panels was installed on the roof, covering over 370,000 sq. ft – creating one of the largest rooftop solar photovoltaic systems in North America. These bi-facial solar panels generate energy from both sides and optimize the use of direct sunlight and light reflected from the white roof surface.
Recloser
G&W Electric Viper-ST Reclosers participate in an automatic throwover scheme to transfer the campus to an alternate power source within 5 to 12 seconds in the case of the loss of the primary feeder. A flywheel ensures no detectable loss in power during this switch.
Switchgear
The G&W Electric Trident-SR with SafeVu is a 15.5 kV class switchgear that performs a 3-4 cycle operation (open or close). The three switches are operated in a FLISR (Fault Location, Isolation and Service Restoration) loop scheme using ABB REC670 relays – providing power to the campus using utility, solar array and energy (battery) storage as the main sources.
Flywheel
A flywheel is one of the most critical components of the whole system. When energy is being stored, electricity drives the motor that spins the flywheel. When the stored energy is being recovered, the motor acts as a generator to convert the spinning motion back to electricity.
The heavy mass of the flywheel spins at up to 2,800 rotations per minute. The flywheel system will detect an electric supply outage in ¼ cycle, instantly providing 1MW of backup power to critical loads for up to 68 seconds, giving time for the battery or generator to kick in.
Diesel Generator
A two-megawatt diesel generator provides power continuity if the duration of a utility power outage exceeds the capacity of the battery complex. While renewable power sources rely on some uncontrollable factors (i.e., sunlight for solar panels), the generator can produce power for the microgrid when no other energy sources are available.
Battery Complex
The “heart and soul” of the microgrid is the Flow Battery Energy Storage System. It can store power generated by the solar array and diesel generator in the event of an external outage. It has a total capacity of two-megawatts for four hours, or three-megawatts for two hours. It uses a vanadium electrolyte solution, which is both non-degrading and fireproof.
Control Room
The control room allows G&W to control, manage and display all operations of the microgrid. G&W LaZer automation, combined with SurvalentONE ADMS software, captures critical data and is fed to the control room.
POWR:Suite Platform (from Intelligent Generation Software)
Built on the Google Cloud platform, the POWR:Suite includes Intelligent Generation’s patented algorithms that predict the most profitable use of each resource at every moment, and dispatches it via the site controller. It integrates electric market bids, weather forecasts, asset status and other constraints to optimize its delivery in real-time. POWR:Suite is the engine that maximizes the utility bill savings of an energy storage asset and earns revenue from wholesale power markets.
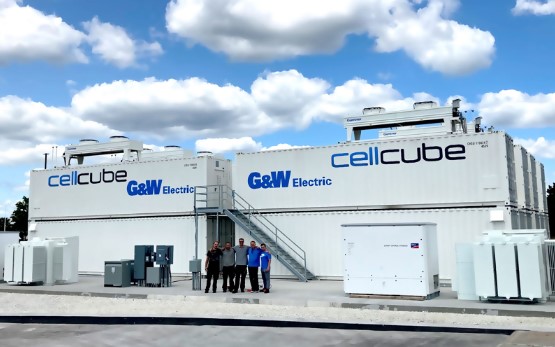
The ”Heart & Soul” of the microgrid is the large battery complex utilizing flow battery technology from CellCube. While several industrial scale battery systems are available, CellCube was chosen because G&W wanted to avoid the potential disposal costs for lithium-ion based systems at the end of the battery life (20 years).
Another huge benefit of this flow battery is that it does not have the risk of thermal runaway, fire, explosion and emissions liabilities that can occur with lithium-ion systems.
The design and implementation of the G&W Electric microgrid was a major project. G&W enlisted the help of outside consultants and contractors to help choose and design the system to meet their requirements. The result is a state-of-the-art system that is scalable to meet the needs of virtually any manufacturing operation.
Electricity needs are different for every manufacturer and custom solutions are required to optimize savings for a microgrid. TDI Energy Solutions works with the consulting team that helped design and operate the G&W microgrid. Call us today at 630-343-0971 to discuss how such a microgrid can be tailored to your specific requirements.
Copyright 2024 TDI Energy Solutions